Dive Deep: Insights About Aluminum Casting Processes
Wiki Article
Unlocking the Potential of Aluminum Spreading: Proven Strategies for Success
Aluminum casting has long been recognized for its adaptability and prevalent applications across different sectors - about aluminum casting. Nevertheless, uncovering the full potential of this procedure calls for greater than just fundamental knowledge. By executing tested strategies sharpened through years of sector experience and development, producers can boost their aluminum casting procedures to brand-new elevations of efficiency and high quality. From enhancing style factors to consider to improving manufacturing procedures, the essential lies in utilizing these approaches successfully. Join us as we check out the crucial elements that can propel aluminum spreading in the direction of unequaled success in today's open market landscape.Advantages of Light Weight Aluminum Spreading
Aluminum casting supplies a wide variety of benefits that make it a preferred selection in different industrial applications. One of the main benefits of light weight aluminum casting is its light-weight nature, which adds to sustain efficiency in industries such as automotive and aerospace. In addition, aluminum is highly flexible, allowing for complex and complex forms to be quickly created with casting processes. This adaptability in style is a significant benefit for markets that require parts with particular geometries.Moreover, light weight aluminum spreading supplies exceptional corrosion resistance, making it ideal for applications where exposure to harsh environments is a concern. The material additionally exhibits excellent thermal conductivity, which is helpful for markets needing warm dissipation, such as electronics (about aluminum casting). Light weight aluminum is fully recyclable, straightening with the growing emphasis on lasting practices in modern manufacturing.
Design Considerations for Casting
When thinking about casting style, thorough interest to information is extremely important to guarantee the successful production of high-grade components. The design stage plays a critical duty in the total success of a light weight aluminum spreading task. One crucial consideration is the choice of suitable geometries and features that assist in the spreading procedure. Designers should consider aspects such as draft angles, fillets, and wall surface density to guarantee appropriate metal flow and solidification during casting.Additionally, factors to consider associated with parting lines, gating systems, and risers are necessary to stop issues like porosity and contraction. It is vital to optimize the layout for reliable material use and minimize post-processing demands. Simulations and prototyping can be important tools in assessing and refining the spreading layout before full-scale production.
Collaboration in between layout designers, foundries, and suppliers is essential to deal with any kind of prospective difficulties early in the layout phase. By including these factors to consider right into the spreading layout process, producers can enhance item high quality, reduce costs, and eventually unlock the full potential of aluminum spreading.
Enhancing Casting Performance
Designing with a focus on optimizing product flow and decreasing issues is crucial when aiming to boost casting performance in light weight aluminum Source casting tasks. To achieve this, making use of simulation software application can help in determining possible problems prior to the casting procedure starts. By imitating the flow of liquified aluminum, designers can adjust gating and riser layouts to make certain correct filling and solidification, inevitably decreasing the event of problems such as porosity or contraction.
Moreover, carrying out correct heat click now treatment procedures can boost the overall casting performance. Warmth treatment can assist enhance the mechanical homes of the light weight aluminum casting, guaranteeing that the last part fulfills the required specifications. Furthermore, utilizing automation and robotics in the spreading process can streamline production, reduce manual work, and boost total performance.
Additionally, constant tracking and quality assurance during the casting procedure are crucial for identifying any discrepancies and making sure that the end products fulfill the preferred requirements. By carrying out these approaches, suppliers can enhance casting efficiency, improve item top quality, and inevitably attain higher success in aluminum casting jobs.
Quality Assurance in Light Weight Aluminum Spreading
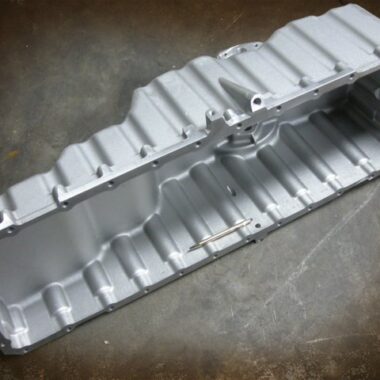
Effective quality assurance practices play a critical duty in guaranteeing the accuracy and reliability of aluminum spreading procedures. Quality control steps in light weight aluminum casting include a variety of tasks focused on supporting details standards and identifying variances that can compromise the end product. These techniques start with the careful selection and assessment of raw products to guarantee their quality and suitability for the casting procedure. Tracking and regulating the criteria of the spreading procedure itself, such as air conditioning, stress, and temperature prices, are vital action in keeping uniformity and honesty in the last items.
In addition to procedure control, quality control in aluminum spreading involves strenuous testing and examination procedures at different phases of manufacturing. By executing durable top quality control practices, light weight aluminum casting centers can supply products that meet client assumptions for performance, dependability, and high quality.
Optimizing Productivity
To achieve ideal monetary efficiency, a thorough approach for making the most of earnings within light weight aluminum spreading procedures have to be meticulously devised and performed. One essential aspect of taking full advantage of earnings in light weight aluminum spreading is enhancing manufacturing effectiveness. This includes improving processes, decreasing waste, and reducing downtime to make certain that resources are utilized properly. Applying lean production concepts can help identify locations for renovation and enhance general operational performance.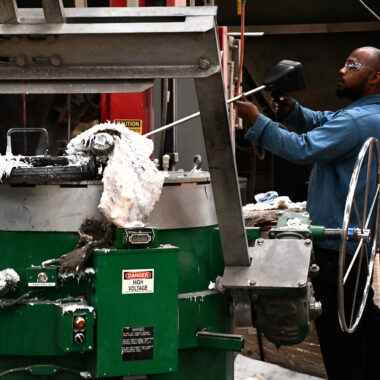
In addition, expanding item offerings and discovering brand-new markets can assist increase revenue streams. Understanding consumer demands and market fads can assist calculated decisions to maximize emerging chances. Buying r & d to innovate processes or products can additionally drive earnings through distinction and customer fulfillment.
Conclusion
Finally, aluminum spreading uses many advantages in terms of layout resilience, flexibility, and cost-effectiveness. By carefully taking into consideration style factors to consider, improving visit the site casting efficiency, applying high quality control measures, and maximizing earnings, manufacturers can open the full capacity of light weight aluminum spreading. This flexible and reliable process has actually shown to be an effective choice for a wide variety of commercial applications.Additionally, aluminum is very malleable, enabling for complex and complex forms to be conveniently produced with spreading processes.Effective high quality control techniques play a pivotal function in making certain the precision and dependability of light weight aluminum casting processes.In addition to procedure control, top quality control in light weight aluminum spreading involves rigorous testing and assessment treatments at numerous stages of production. By executing robust high quality control techniques, light weight aluminum casting facilities can provide items that satisfy consumer assumptions for performance, quality, and reliability.
By thoroughly thinking about style considerations, improving casting effectiveness, executing quality control procedures, and making the most of success, manufacturers can unlock the complete capacity of aluminum casting.
Report this wiki page